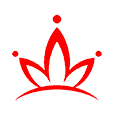
Menu
BS Wire and Cable Fire Resistance Tester is suitable for fire resistance test, water spray fire resistance test and mechanical fire resistance test. It is suitable for mineral insulated cable with rated voltage not exceeding 450/750V. It keeps the circuit intact for a long time under flame conditions. It complies with British Fireproof Cable Standard BS6387 “Guidelines for Maintaining Circuit Performance of Cables in Case of Fire”. The test machine simultaneously meets the BS8491 standard for assessing fire integrity of large diameter cables as a component using the smoke and heat control system given BS7346-6, and identifying other activities of the fire safety system. It is suitable for cables with a cable rated voltage not exceeding 600/1 000 V and an outer diameter greater than 20 mm.
Standard:
BS6387 2013
BS8491: 2008
GB/T19216
Technical parameters
A 650℃±40℃ -3H
B 750℃±40℃ -3H
C 950℃±40℃-3H
S 950℃±40℃-20Min
Let current go through all the cores of cable when in test, three single phase transformers, and has enough ability to keep max allowable leakage current of 3A under test voltage. Each core of cable in the other end connects with a lamp, and load current of 0.25A under rated voltage.
Let current go through all the cores of cable when in test, three single phase transformers, and has enough ability to keep max allowable leakage current of 3A under test voltage. Each core of cable in the other end connects with a lamp, and load current of 0.25A under rated voltage.
X 650±40℃
Y 750±40℃
Z 950±40℃
Specification: